Ensuring Safe Delivery: The Process of Packing and Shipping Glass Products at Palace of Glass
At Palace of Glass, we understand that the beauty and functionality of our custom glass products are only fully realized when they arrive safely at your destination. Glass, while elegant and versatile, is inherently fragile, and its transportation requires meticulous attention to detail. After the order is complete we will provide detailed visual report with photos and sometimes videos. After your confirmation your glass products are ready for packing and shipping! From the moment your custom glass piece leaves our facility, we take every precaution to ensure it reaches you in pristine condition. This article explains our comprehensive process of packing and shipping glass products, highlighting the steps we take to protect your investment.
The Importance of Safe Packing and Shipping
Shipping glass is a delicate operation, and the risks associated with it are significant. A single scratch, chip, or crack can compromise the entire piece, rendering it unusable. At Palace of Glass, we are committed to delivering not just a product, but an experience—one that begins the moment you open your package and see your custom glass creation exactly as you envisioned it. Our rigorous packing and shipping protocols are designed to mitigate risks and guarantee that your glass products arrive in perfect condition, no matter how far they need to travel.
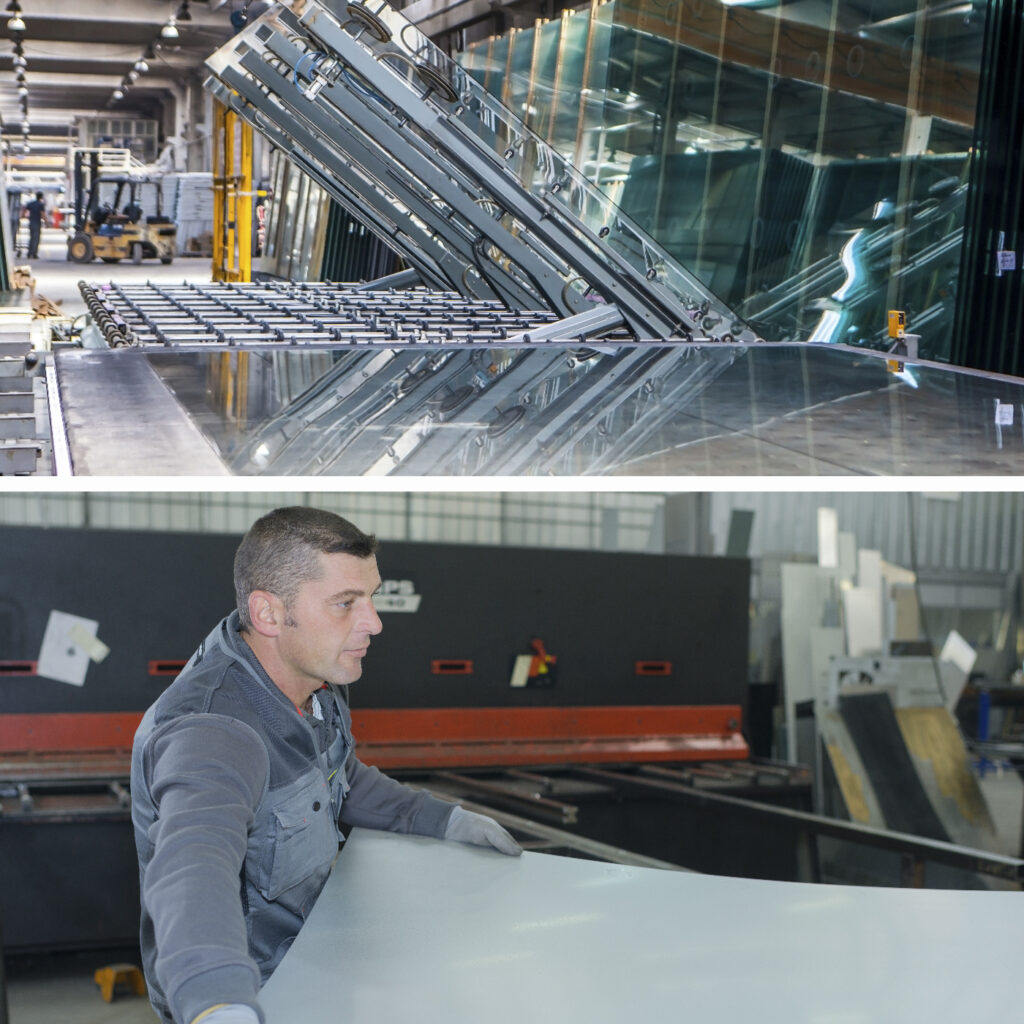
Step 1: Wrapping the Glass for Protection
The first step in our packing process is to wrap the glass in protective plastic. This layer serves as the initial defense against scratches, dust, and other particles that could mar the surface of the glass. By enveloping the glass in a soft yet durable plastic film, we ensure that the delicate surface remains flawless during handling and transportation.
The wrapping process is done in a dust-free environment to prevent any particles from becoming trapped between the plastic and the glass surface. This attention to detail is crucial in maintaining the integrity of the glass and ensuring that it arrives at your location without any cosmetic imperfections.
Step 2: Securing the Corners with Protective Foam
Once the glass is wrapped, the next step is to secure its corners with protective foam. Corners are the most susceptible to impact damage during transportation and loading, so we use high-density foam padding to absorb any shocks or vibrations that the glass may encounter along the way.
The foam padding is custom-cut to fit the exact dimensions of your glass piece, ensuring that it stays securely in place throughout the journey. This cushioning not only protects the corners from direct impacts but also helps to distribute any forces evenly across the surface of the glass, further reducing the risk of damage.
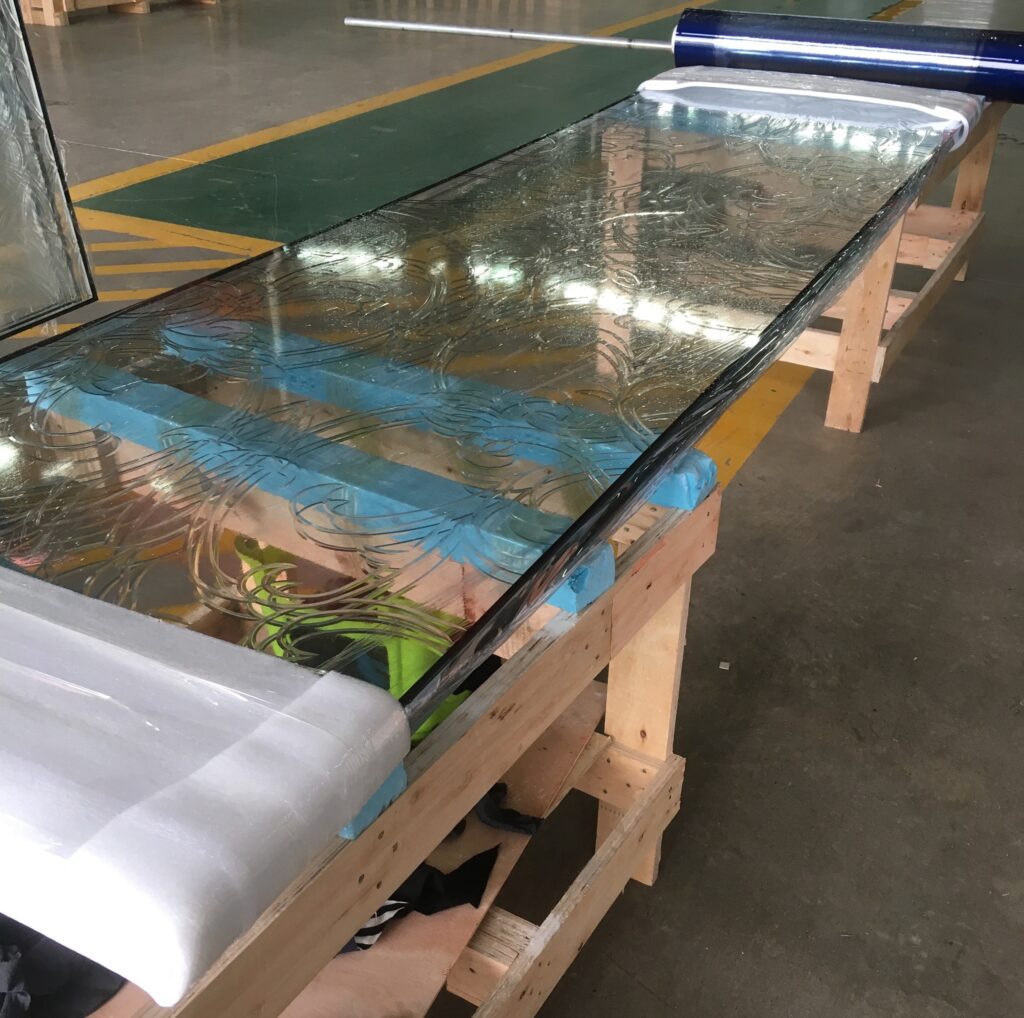
Step 3: Packing and Shipping the Glass in Custom Wooden Crates
After the glass is wrapped and its corners are secured, it is time to pack the units tightly in custom-built wooden crates. These crates are specially designed to provide maximum protection during transit. Depending on the size and shape of the glass, as well as the size of the order, we use different types of crates to ensure the best possible fit and stability.
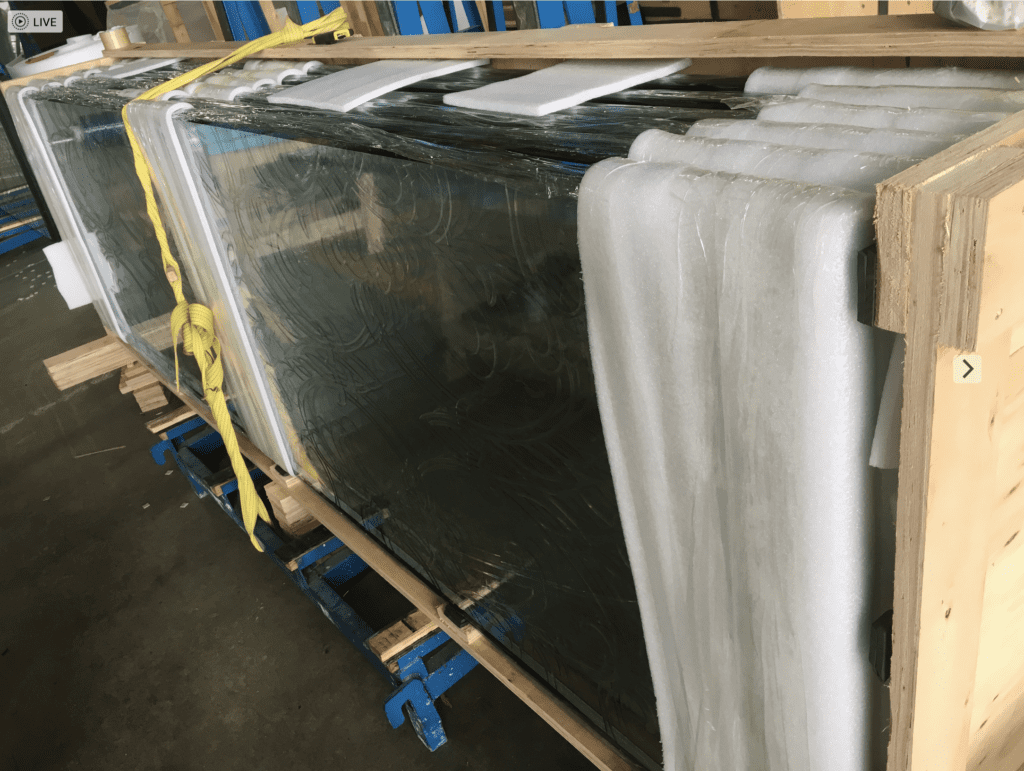
For larger glass panels or bulk orders, we often use A-frame shaped wooden crates. These crates allow the glass to be packed standing upright, which is the safest position for large sheets of glass. The A-frame design also provides extra stability, preventing the glass from shifting during transportation.
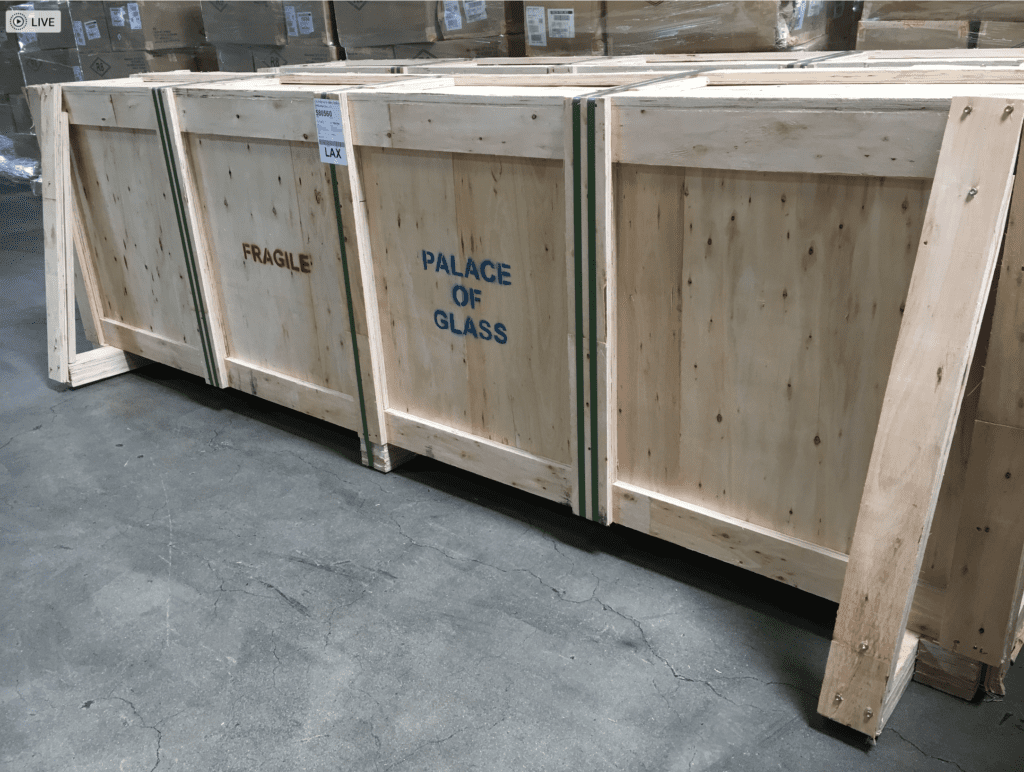
For smaller or more delicate items, we use box-shaped crates with the glass standing upright inside. These crates are built with precision to ensure that the glass fits snugly, eliminating any movement within the crate. The inside of each crate is lined with additional padding materials to provide an extra layer of protection against bumps and jolts.
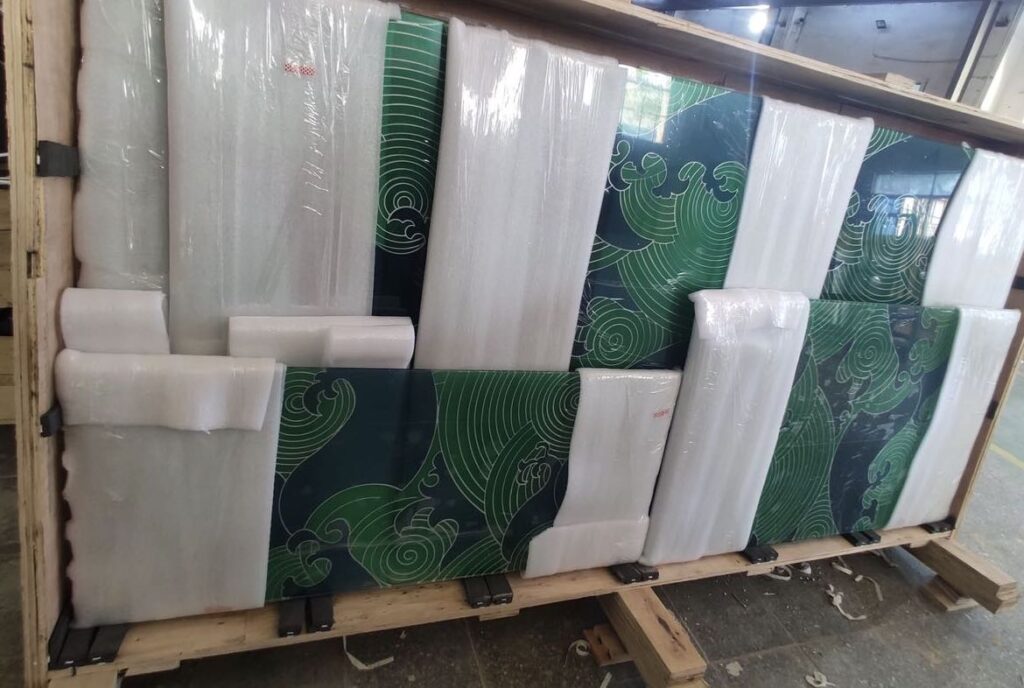
Step 4: Designing Crates for Easy Loading and Transport of your Glass Order
Our wooden crates are not only designed to protect the glass during transportation but also to facilitate easy loading and unloading. Each crate is constructed with forklift access points, allowing for seamless dock loading. This feature is especially important for larger shipments, as it reduces the handling required and minimizes the risk of accidental drops or impacts.
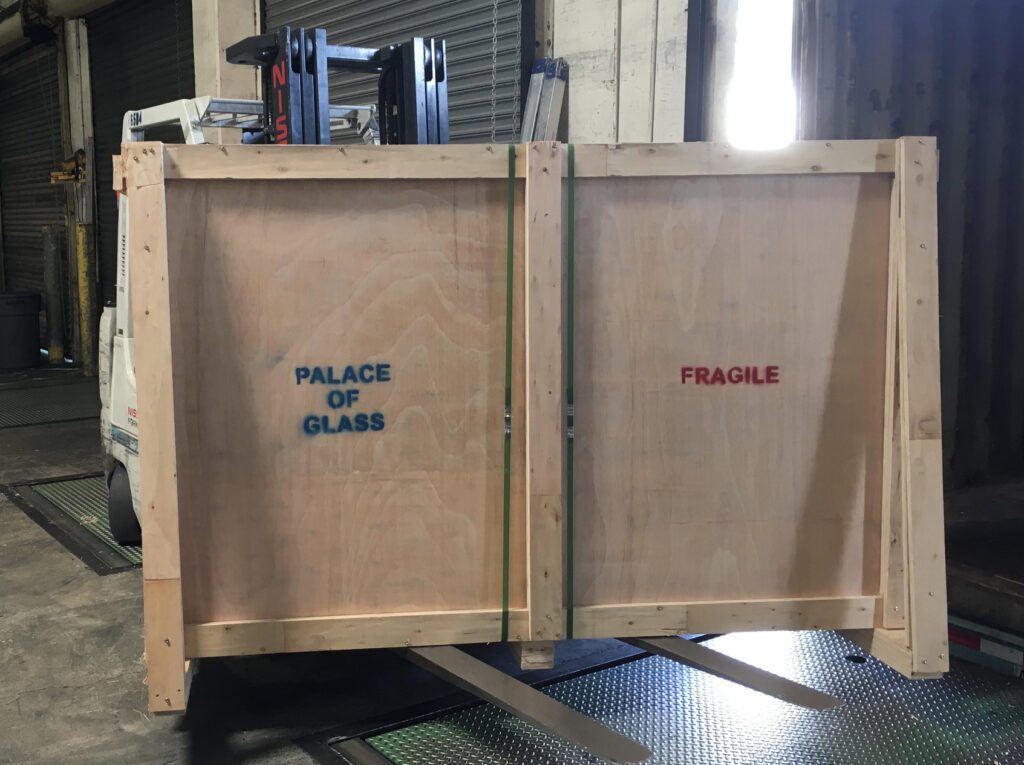
In addition to being functional, our crates are clearly marked with warning labels to ensure that everyone involved in the shipping process is aware of the fragile nature of the contents. These markings include “Fragile,” “Handle with Care,” “This Side Up” ,” Do Not Stack”,” Glass Do Not Drop” and usually the destination address posted on the box along with the PRO number. All these indicators help prevent mishandling during transit.
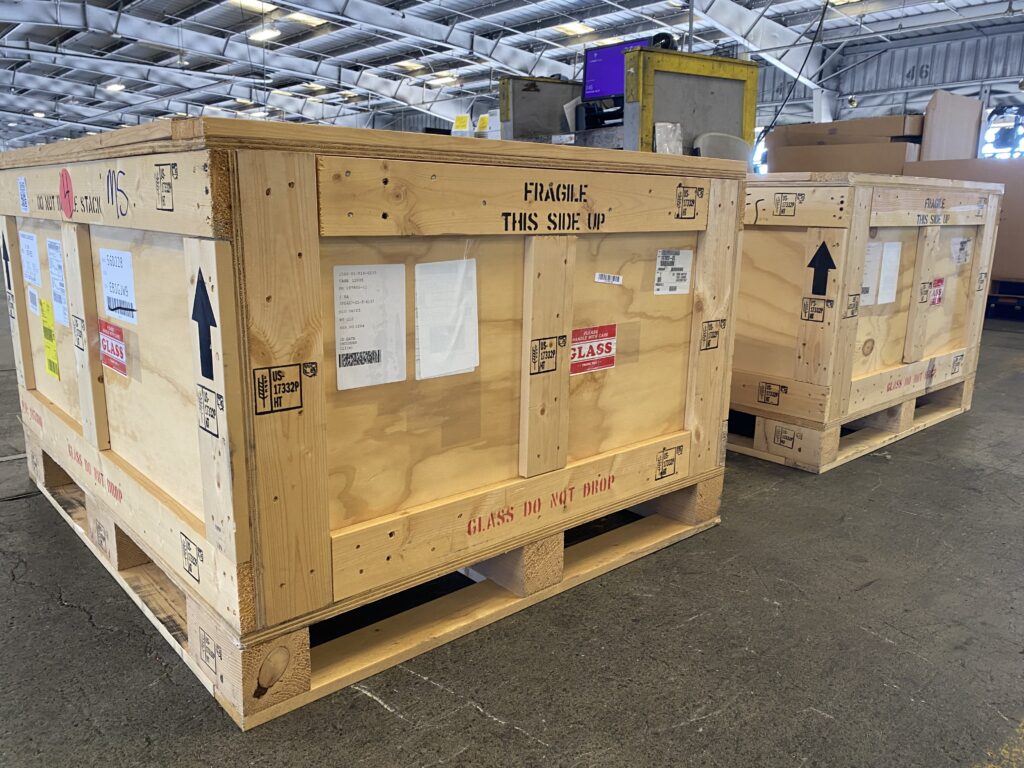
Small Glass items like Glass Jewelry or Gift items usually packed as individual units into cardboard boxes and then into wooden crates,
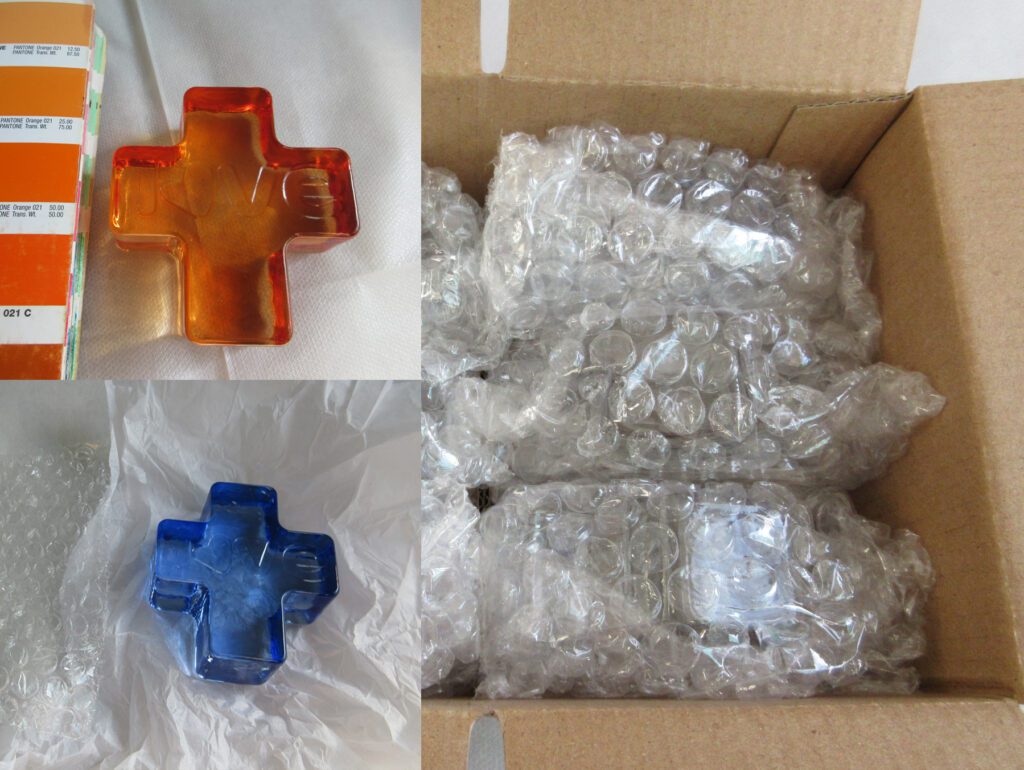
Step 5: Selecting the Right Carrier for Your Order
Palace of Glass has established relationships with numerous land carriers and trucking companies, allowing us to offer you a range of shipping options at competitive rates. When your order is crated and ready for shipment, we will provide you with various carrier options, each tailored to your specific needs in terms of cost, delivery speed, and service quality.
Once a carrier is selected, we coordinate with them to ensure that your shipment is handled with the utmost care. All of our shipments are insured under carrier liability, providing you with peace of mind that your investment is protected. For additional security, we also offer the option to purchase third-party insurance, which can cover the full value of your glass products in the unlikely event of damage during transit.
Finalizing Your Order and Preparing for Shipment
Before your order is shipped, we conduct a final visual confirmation with you, the client, to ensure that everything meets your expectations. This step is crucial in maintaining transparency and guaranteeing that the product you receive is exactly what you ordered.
Please note that all orders must be paid in full before they are shipped. At Palace of Glass, we do not accept credit cards for the forms of payment, we can take checks or bank wires only. This policy is in place to protect both our clients and our company, ensuring that all transactions are secure and that there are no delays in processing your order.
Standard Lead time depends on the scope of the order, usually 8-10 weeks. The counting of the production time begins when the sketches are confirmed and the deposit is made.
Conclusion
At Palace of Glass, we take great pride in the craftsmanship of our custom glass products, and we extend that same level of care to the packing and shipping process. By following a meticulous packing procedure—wrapping the glass, securing the corners, and custom-building protective crates—we ensure that your glass products arrive safely and in perfect condition. Our partnerships with trusted carriers and our commitment to providing insured shipments further enhance the security and reliability of our services.
When you choose Palace of Glass, you can rest assured that your custom glass creations will be delivered with the same precision and attention to detail that went into their design and fabrication. Your satisfaction is our top priority, and we are dedicated to making sure that your glass products arrive at your destination exactly as you envisioned them.
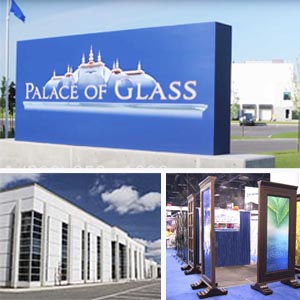